Destylator przemysłowy to zaawansowane urządzenie, które służy do oddzielania składników mieszanin cieczy na podstawie różnic w ich temperaturach wrzenia. Proces ten jest kluczowy w wielu branżach, takich jak przemysł chemiczny, petrochemiczny czy spożywczy. W destylacji wykorzystuje się zjawisko parowania, gdzie ciecz podgrzewana do określonej temperatury zaczyna przechodzić w stan gazowy. Następnie para jest schładzana i kondensowana z powrotem do stanu ciekłego, co pozwala na uzyskanie czystszych frakcji. W przemyśle chemicznym destylatory są używane do produkcji rozpuszczalników, alkoholi oraz innych substancji chemicznych. W przemyśle petrochemicznym proces ten jest niezbędny do rafinacji ropy naftowej, gdzie oddziela się różne frakcje, takie jak benzyna, olej napędowy czy nafta. W branży spożywczej destylatory wykorzystywane są do produkcji wysokoprocentowych alkoholi, takich jak wódka czy whisky, a także do ekstrakcji aromatów i olejków eterycznych z roślin.
Jakie są rodzaje destylatorów przemysłowych i ich cechy
W świecie przemysłowym istnieje wiele rodzajów destylatorów, które różnią się konstrukcją oraz zastosowaniem. Najpopularniejsze z nich to destylatory prostokątne, kolumnowe oraz wirówkowe. Destylatory prostokątne charakteryzują się prostą budową i są często stosowane w mniejszych zakładach produkcyjnych. Ich zaletą jest łatwość obsługi oraz niskie koszty eksploatacji. Z kolei destylatory kolumnowe są bardziej skomplikowane i efektywne, co sprawia, że są preferowane w dużych zakładach przemysłowych. Dzięki zastosowaniu kolumny rektyfikacyjnej umożliwiają one uzyskanie wyższej czystości produktów końcowych oraz lepszą separację składników. Destylatory wirówkowe natomiast wykorzystują siłę odśrodkową do oddzielania składników mieszaniny, co czyni je idealnymi do procesów wymagających szybkiej separacji.
Jakie są kluczowe elementy konstrukcyjne destylatora przemysłowego
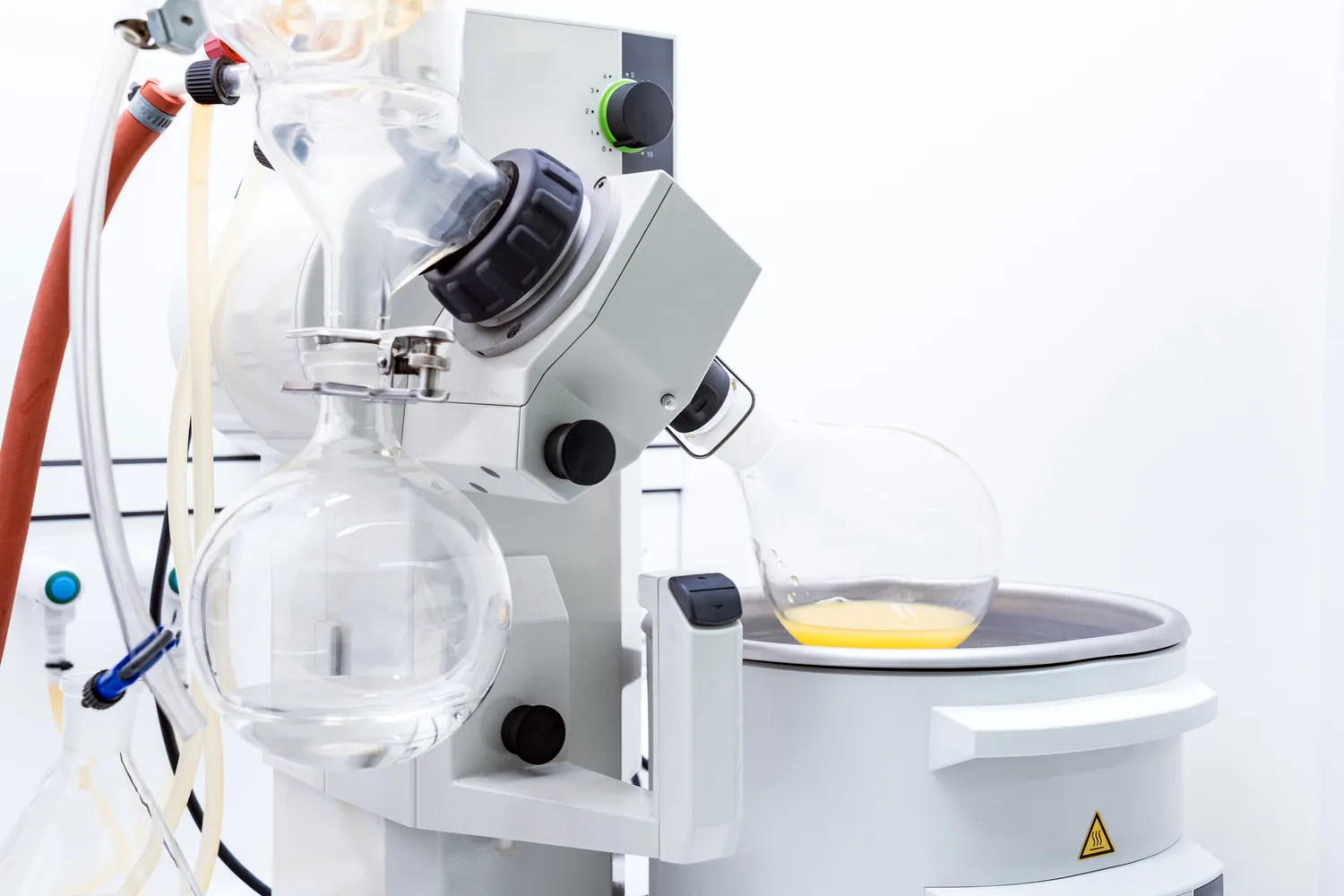
Każdy destylator przemysłowy składa się z kilku kluczowych elementów konstrukcyjnych, które współpracują ze sobą w celu efektywnego przeprowadzenia procesu destylacji. Podstawowym elementem jest zbiornik grzewczy, który podgrzewa ciecz do wymaganej temperatury wrzenia. W przypadku destylatorów kolumnowych istotnym elementem jest kolumna rektyfikacyjna, która umożliwia wielokrotne skraplanie i parowanie cieczy, co zwiększa efektywność separacji składników. Kolejnym ważnym komponentem jest skraplacz, który schładza parę i przekształca ją z powrotem w ciecz. Dodatkowo wiele nowoczesnych destylatorów wyposażonych jest w systemy automatyzacji oraz monitorowania parametrów procesu, co pozwala na precyzyjne sterowanie i optymalizację pracy urządzenia. Ważnym aspektem jest również izolacja termiczna zbiorników oraz rur transportowych, co minimalizuje straty ciepła i zwiększa efektywność energetyczną całego systemu.
Jakie są korzyści z używania nowoczesnych destylatorów przemysłowych
Nowoczesne destylatory przemysłowe oferują szereg korzyści, które przyczyniają się do zwiększenia efektywności procesów produkcyjnych oraz poprawy jakości końcowych produktów. Jedną z głównych zalet jest wysoka wydajność energetyczna, dzięki zastosowaniu innowacyjnych technologii grzewczych oraz systemów recyklingu ciepła. To pozwala na znaczne obniżenie kosztów operacyjnych związanych z zużyciem energii. Ponadto nowoczesne urządzenia często wyposażone są w zaawansowane systemy automatyzacji, które umożliwiają precyzyjne monitorowanie i kontrolowanie parametrów procesu w czasie rzeczywistym. Dzięki temu można szybko reagować na zmiany warunków pracy oraz optymalizować procesy produkcyjne. Kolejną korzyścią jest możliwość uzyskania wyższej czystości produktów końcowych dzięki zastosowaniu technologii rektyfikacji oraz wielostopniowej separacji składników. Nowoczesne destylatory są także bardziej przyjazne dla środowiska dzięki zmniejszonej emisji szkodliwych substancji oraz niższemu zużyciu surowców naturalnych.
Jakie są najczęstsze problemy związane z destylatorami przemysłowymi
Destylatory przemysłowe, mimo swojej zaawansowanej technologii, mogą napotykać różne problemy, które wpływają na ich wydajność oraz jakość produkcji. Jednym z najczęstszych problemów jest zatykanie kolumn rektyfikacyjnych, co może prowadzić do obniżenia efektywności separacji składników. Zatykanie to często spowodowane jest osadzaniem się zanieczyszczeń lub produktów ubocznych w procesie destylacji. Innym istotnym problemem jest nieprawidłowe ustawienie parametrów procesu, takich jak temperatura czy ciśnienie, co może prowadzić do nieefektywnej separacji i obniżonej jakości produktów końcowych. W przypadku destylatorów kolumnowych, niewłaściwe rozłożenie przepływu cieczy w kolumnie może również powodować problemy z efektywnością. Dodatkowo, awarie systemów grzewczych mogą prowadzić do przestojów w produkcji oraz zwiększenia kosztów operacyjnych. Regularne konserwacje oraz monitorowanie stanu technicznego urządzeń są kluczowe dla minimalizacji ryzyka wystąpienia tych problemów.
Jakie są trendy w rozwoju technologii destylacji przemysłowej
W ostatnich latach można zaobserwować wiele interesujących trendów w rozwoju technologii destylacji przemysłowej, które mają na celu zwiększenie efektywności oraz zmniejszenie wpływu na środowisko. Jednym z kluczowych kierunków jest automatyzacja procesów destylacyjnych, która pozwala na precyzyjne sterowanie parametrami pracy urządzeń oraz minimalizację błędów ludzkich. Dzięki zastosowaniu nowoczesnych systemów monitorowania i analizy danych możliwe jest optymalizowanie procesów w czasie rzeczywistym, co przekłada się na wyższą jakość produktów końcowych oraz niższe koszty operacyjne. Kolejnym ważnym trendem jest rozwój technologii wykorzystujących odnawialne źródła energii do zasilania destylatorów, co przyczynia się do zmniejszenia emisji gazów cieplarnianych oraz obniżenia kosztów energii. Wiele firm inwestuje także w badania nad nowymi materiałami i konstrukcjami kolumn rektyfikacyjnych, które pozwalają na jeszcze lepszą separację składników oraz zwiększenie wydajności procesów.
Jakie są wymagania dotyczące bezpieczeństwa w pracy z destylatorami przemysłowymi
Bezpieczeństwo pracy z destylatorami przemysłowymi jest kluczowym aspektem, który należy uwzględnić na każdym etapie eksploatacji tych urządzeń. Przede wszystkim konieczne jest przestrzeganie norm i przepisów dotyczących bezpieczeństwa pracy, które regulują m.in. sposób instalacji, obsługi oraz konserwacji destylatorów. Pracownicy powinni być odpowiednio przeszkoleni w zakresie obsługi urządzeń oraz znajomości procedur awaryjnych. Ważnym elementem jest również regularne przeprowadzanie przeglądów technicznych oraz konserwacji sprzętu, co pozwala na wykrycie potencjalnych usterek zanim staną się one zagrożeniem dla zdrowia i życia pracowników. W kontekście bezpieczeństwa istotne jest także zapewnienie odpowiedniej wentylacji w pomieszczeniach, gdzie znajdują się destylatory, aby uniknąć gromadzenia się szkodliwych oparów chemicznych. Dodatkowo stosowanie odpowiednich środków ochrony osobistej przez pracowników, takich jak rękawice czy okulary ochronne, jest niezbędne dla minimalizacji ryzyka urazów.
Jakie są koszty inwestycji w destylatory przemysłowe
Koszty inwestycji w destylatory przemysłowe mogą znacznie różnić się w zależności od wielu czynników, takich jak typ urządzenia, jego wydajność oraz stopień zaawansowania technologicznego. Na początku warto zwrócić uwagę na koszt zakupu samego urządzenia, który może wynosić od kilku tysięcy do nawet milionów złotych w przypadku dużych instalacji przemysłowych. Oprócz ceny zakupu należy uwzględnić także koszty instalacji oraz uruchomienia destylatora, które mogą obejmować prace budowlane, elektryczne oraz hydrauliczne. Koszty eksploatacyjne to kolejny istotny aspekt inwestycji; obejmują one zużycie energii elektrycznej czy paliwa do podgrzewania cieczy oraz koszty związane z konserwacją i serwisowaniem urządzenia. Warto także pamiętać o kosztach związanych z zatrudnieniem wykwalifikowanego personelu do obsługi destylatora oraz ewentualnymi szkoleniami dla pracowników.
Jakie są alternatywy dla tradycyjnej destylacji przemysłowej
W ostatnich latach pojawiły się różnorodne alternatywy dla tradycyjnej destylacji przemysłowej, które oferują nowe podejścia do separacji składników mieszanin cieczy. Jedną z takich metod jest ekstrakcja cieczy ciekłą (LLE), która polega na wykorzystaniu rozpuszczalników do oddzielania składników na podstawie ich rozpuszczalności. Ta metoda może być bardziej efektywna w przypadku substancji o podobnych temperaturach wrzenia lub gdy tradycyjna destylacja nie daje oczekiwanych rezultatów. Inną alternatywą jest membranowa separacja gazu lub cieczy, która wykorzystuje specjalne membrany do oddzielania składników na podstawie ich wielkości cząsteczek lub właściwości chemicznych. Technologia ta staje się coraz bardziej popularna ze względu na swoją efektywność energetyczną i niskie koszty operacyjne. Również chromatografia jest stosowana jako alternatywa dla tradycyjnej destylacji; umożliwia ona separację składników na podstawie ich interakcji z fazą stacjonarną i mobilną.
Jakie są przyszłe kierunki rozwoju technologii destylacyjnej
Przyszłość technologii destylacyjnej zapowiada się obiecująco dzięki ciągłemu rozwojowi innowacyjnych rozwiązań oraz badań naukowych w tej dziedzinie. Jednym z głównych kierunków rozwoju będzie dalsza automatyzacja procesów produkcyjnych, co pozwoli na jeszcze większą precyzję i efektywność działania destylatorów przemysłowych. Technologie sztucznej inteligencji i uczenia maszynowego będą coraz częściej wykorzystywane do analizy danych procesowych oraz optymalizacji warunków pracy urządzeń w czasie rzeczywistym. Ponadto rosnące zainteresowanie ekologicznymi rozwiązaniami sprawi, że producenci będą dążyć do opracowania bardziej zrównoważonych metod produkcji, które zmniejszą negatywny wpływ na środowisko naturalne. Inwestycje w badania nad nowymi materiałami konstrukcyjnymi kolumn rektyfikacyjnych mogą prowadzić do stworzenia bardziej efektywnych systemów separacyjnych o mniejszych stratach energii i surowców.